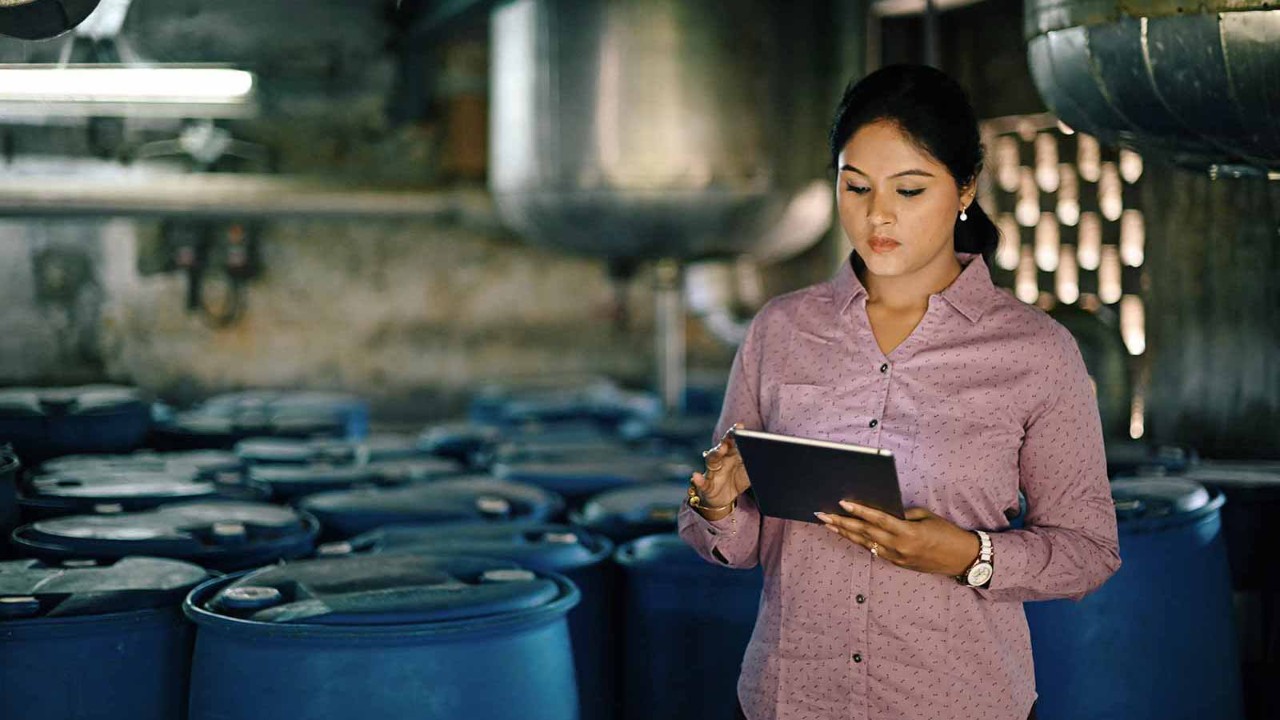
Supply chain challenges are widespread and experienced by many industries globally. They affect small businesses, retail outlets, giant manufacturing facilities and trading units alike.
In India, the challenges are numerous, including the need to keep transport costs low, meet customers’ demands in a timely way, source optimum transport capacity, provide efficient delivery services, and more. Currently, the increase in e-commerce in the region has added to the existing supply chain problems.
Your business clients may benefit from considering some of the following ways in which businesses in India are currently preparing for these challenges and keeping their operations running smoothly.
The reorder level has to be defined meticulously, factoring in lead time, geo-economic conditions, etc
Inventory tracking
India is a consumer-based economy, so inventory – and carrying costs – can be huge, particularly in the fast-moving consumer goods sector, and supply chain problems can quickly become intractable. It is critical for businesses to know their customers’ preferences, seasonal requirements, location-specific needs, etc, and to calculate the reorder levels needed to reduce the supply chain management issues. The reorder level has to be defined meticulously, factoring in lead time, geo-economic conditions, availability of material, etc.
Even during the best of times, it is important to track inventory. With frequent supply chain shortages, it is absolutely essential to know what is in stock and what needs replenishing. When dealing with high volumes of inventory, businesses cannot afford to be caught off guard.
Your business clients should also be mindful of the carrying cost of inventory, which makes knowing the reorder level critical. Factoring in the lead time for inventory reordering (including measures to mitigate issues arising from disrupted logistics) is a must.
Popular products
Smaller businesses face particular challenges when it comes to supply chain matters. It is not always possible for them to invest in a huge amount of inventory with limited resources. In addition to budgetary concerns, limitations on inventory investment include time considerations, labour and how much physical space a business has available.
Some of the ways small businesses can deal with this are:
- to buy as much as they can afford when a popular product becomes available
- to look for heavily discounted items to stock up at reorder level
- to seek financing to invest in popular inventory
- to expand their storage space or consider renting some
- to consider outsourcing solutions for storage, packing and shipping.
In India, space management is a big factor in managing the supply chain. It is a densely populated country, so adequate warehouse capacity is a challenge. But with renting and managing a warehouse costly, many businesses are focusing on procuring popular products when they are at their cheapest and storing them in a rented premises for future sale.
Alternatives
With an unpredictable supply chain, certain products can become unavailable at short notice. Businesses need to consistently look at alternative suppliers, preferably in different locations. That way, they can maintain stock levels even if a particular supplier is unable to fulfil their needs.
In addition, businesses can be creative in their offerings to customers. For example, a restaurant or food-related business can research alternative ingredients and dishes to put on the menu. Customers in India will not mind the substitution if it matches the taste and suits the pocket.
Efficient tools
Businesses are increasingly using automation tools to help stay on top of the supply chain requirements and plan efficiently. Supply chain management (SCM) software is mainly used by larger businesses, which may be dealing with multiple departments, locations and niche markets. However, smaller companies can also benefit from SCM, especially when supply chain issues are common.
SCM software tracks inventory, manages shipping and offers updates on which items are moving the fastest.
Honesty
Supply chain issues are getting quite a bit of press lately, so most businesses’ customers are likely aware that certain items may not be available or may take longer to ship. The best policy here is to be transparent about this with customers. This could mean businesses explaining on their company website that orders may be delayed due to circumstances beyond their control, but that they are doing everything possible to reduce delays.
If there are any challenges with certain products, the best policy is to let people know about this before placing orders. Customers don’t want to be surprised that something they were expecting to arrive in a few days is now going to take a month or more.
Latest developments
While supply chain disruptions can occur at any time, they are often predictable. They may be caused by politics, economic factors or weather conditions. Keep up to date with trends in the industry and with news affecting the products the business needs.
If a likely shortage can be anticipated, appropriate steps can be taken. Businesses won’t always be able to predict every future disruption, but they can prevent some problems by keeping up with the latest developments.
Disruption-ready
Going forward, many issues – such as climate change, political instability in various parts of the world and the ongoing pandemic – may continue to cause disruptions. However, promising developments such as blockchain management of supply chains may offer creative solutions in the near future.
Your business clients should take a multipronged approach to prepare for any disruption.
More information
ACCA’s Practice Connect hub has resources, insights and innovative tools to help your practice stay ahead and relevant in a fast-changing business landscape